What are the problems that need to be paid attention to during the production of PCBA?
The choice of PCBA through tin in the PCBA production process is also critical. In the through-hole plug-in process, the PCB is not well-transferred, which is prone to problems such as soldering, tin cracking, and even missing parts.
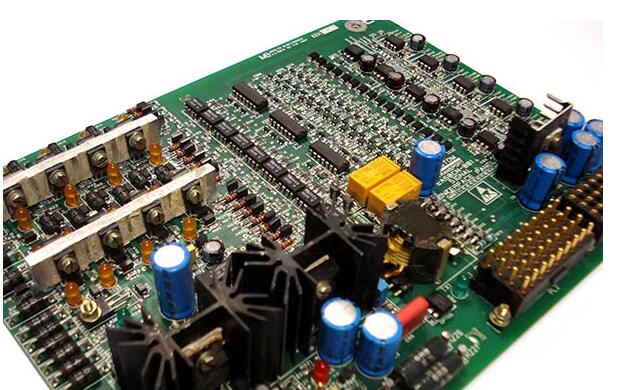
We should understand these two big points about PCBA through tin:
First, PCBA through tin requirements
According to the IPC standard, the PCBA through-hole soldering requirements of the through-hole solder joints are generally above 75%, that is to say, the solder-on-board surface appearance inspection is not less than 75% of the aperture height (plate thickness), PCBA Tin plating is suitable from 75% to 100%. The plated through hole is connected to the heat dissipation layer or the heat conduction layer for heat dissipation, and the PCBA requires more than 50%.
Second, the factors affecting the penetration of PCBA
PCBA poor tin penetration is mainly affected by factors such as materials, wave soldering processes, fluxes, and hand soldering.
Specific analysis of factors affecting PCBA penetration:
1, material
High-temperature melting tin has strong permeability, but not all welded metal (PCB board, components) can penetrate into it. For example, aluminum metal, its surface will automatically form a dense protective layer, and the internal molecules The difference in structure also makes it difficult for other molecules to penetrate. Second, if there is an oxide layer on the surface of the metal to be welded, it will also prevent the penetration of molecules. We usually use flux treatment or gauze to clean it.
2, wave soldering process
The poor PCBA penetration is directly related to the wave soldering process, re-optimizing the poor soldering parameters such as wave height, temperature, soldering time or moving speed. First, the orbital angle is appropriately lowered, and the height of the peak is increased to increase the contact between the liquid tin and the soldered end. Then, the temperature of the wave soldering is increased. Generally, the higher the temperature, the stronger the permeability of tin, but this should be considered. The temperature of the components can withstand; finally, the speed of the conveyor belt can be reduced, the preheating and welding time can be increased, and the flux can fully remove the oxide, infiltrate the welding end, and increase the amount of tin to be eaten.
3, flux
Flux is also an important factor affecting the poor soldering of PCBA. Flux mainly plays the role of removing the surface oxide of PCB and components and preventing reoxidation during soldering. The flux is not well selected, the coating is uneven, and the amount is too small. Both will lead to poor tin penetration. The well-known brand of flux can be selected, the activation and infiltration effects will be higher, and the oxides that are difficult to remove can be effectively removed. The flux nozzles should be inspected, and the damaged nozzles should be replaced in time to ensure that the surface of the PCB board is coated with an appropriate amount of flux. Use the fluxing effect of the flux.
4, manual welding
In the actual plug-in welding quality inspection, a considerable part of the weldment only has the surface solder formed into a taper, and there is no tin penetration in the via hole. It is confirmed in the functional test that many of these parts are solder joints, which is more in the manual plug-in. The reason for the soldering is that the temperature of the soldering iron is not appropriate and the soldering time is too short. Poor soldering of PCBA can easily lead to solder joint problems and increase the cost of rework. If the requirements for PCBA through tin are relatively high, the welding quality requirements are strict, and selective wave soldering can be used, which can effectively reduce the problem of poor PCBA penetration.